What are the surface treatment methods of ball valve?
The ball valve has been widely used in industrial applications due to its small flow resistance, a wide range of pressure and temperature use range, good sealing performance, short opening and closing time, easy installation and other advantages. The ball is an important part that plays a key role in the opening and closing function for the ball valve. In order to enhance the sealing performance and hardness of the ball, it is necessary to pre-treat the surface of the ball. So what do you know about common surface treatments for the ball body?
The common treatment methods for the surface of the sphere are electroplating, cold coating, spraying and nitriding. The following is the surface treatment method of the ball I often encounter in my work. It is incomplete, but it is guaranteed to be commonly used.
1. Spray welding of cobalt-based alloy,
which is generally used. The common cobalt-based alloy on the ball valve is STL20,38~40HCR; TL1:48~50HCR;
2. Nitriding.
The essence of nitriding is to infiltrate nitrogen atoms into the surface of the workpiece. Actually, the penetration depth is not easy to control
The surface hardness is also unstable; In the manufacturing process of hard seal ball valve, the key is the grinding between the valve seat ring and the ball. During the grinding process, the nitriding layer is easily worn off or very thin, so that when the valve is really used on the pipeline, the ball is easily scratched by impurities in the medium, affecting the sealing, and even making the torque greater.
3. Spray welding or cold spraying of nickel-based alloys.
The commonly used nickel-based alloys on ball valve balls are NI60 and NI55. The melting point of NI60 and NI55 is 1027 ℃, and spray welding or cold spraying can be used. The thickness of spray welding nickel-based alloy is generally 0.5mm-0.7mm, which can meet the basic use requirements. The actual maximum thickness can reach 2.5mm-3mm. In case of cold spraying, the spraying thickness is
0.15mm~0.18mm。 The hardness after spray welding is generally NI55:50~55 HRC, and NI60:55~60HRC;
4. Nickel plating (ENP) or chromium plating (HCr) on the surface of the ball:
when the ball material is carbon steel and the valve is soft sealed, such as A105, 25, LF2, etc., these materials have poor corrosion resistance, so the surface of the ball must be treated with nickel plating (ENP) or chromium plating (HCr) to avoid spherical corrosion and affect the sealing. When the ball is made of austenitic stainless steel or other similar soft materials, and the sealing ring of the ball valve is made of hard materials such as PEEK, it is recommended that the surface of the ball be plated with nickel (ENP) according to the special requirements, which can be appropriately thickened; The hardness after nickel plating (ENP) or chromium plating (HCr) is generally 600HV~800HV.
5. The surface of the sphere is cold sprayed with tungsten carbide WC:
tungsten carbide is characterized by high hardness and good wear resistance. However, the disadvantage is that the melting point of tungsten carbide is particularly high, about 2870 ℃. The melting point of general metal materials is far lower than that of tungsten carbide, so the process of cold spraying tungsten carbide WC can only be used. The normal thickness of sprayed tungsten carbide WC is 0.15 mm~0.18 mm, which can achieve the ideal surface hardness. If special requirements are met, the thickness can reach 0.5 mm~0.7 mm at most. The thicker the thickness of cold spraying, the lower the surface adhesion. It is not recommended to use a thicker thickness of cold spraying. The hardness of surface cold sprayed tungsten carbide WC is generally 1050HV~1450HV, which is about 70HRC.
The above is from STV Valve Technology Group Co., Ltd,we Supplies Trunnion Ball Valve, Trunnion Ball Valve, You can Buy good quality Trunnion Ball Valve, we are Trunnion Ball Valve distributor & Trunnion Ball Valve Factory from China market.
Customers who need the valve ball can contact us. We will serve you wholeheartedly and look forward to your call.
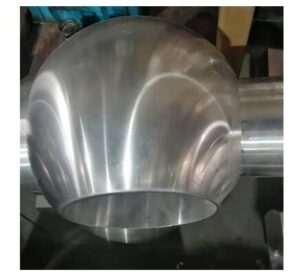
The ball valve has been widely used in industrial applications due to its small flow resistance, a wide range of pressure and temperature use range, good sealing performance, short opening and closing time, easy installation and other advantages.