What is the material of WCB / LCB / LCC / wc6 / WC9 in the valve?
WCB / LCB / LCC / wc6 / wc9 are commonly used materials for valves, but many people don’t know what they mean. Let’s introduce these materials in detail today
W. Wrought casting;
C-carbon steel;
A. B, C indicates the strength value of steel grade from low to high
WCA, WCB and WCC represent carbon steel, ABC represents strength grade, and WCB is commonly used. The pipe material corresponding to WCB shall be A106B and the forging material shall be A105.
Wc6 is a casting of alloy steel, the corresponding pipe material is about a355 P11, and the forging is A182 F11;
wc9, high temperature resistant alloy steel, corresponding to about a355 P22, and forgings corresponding to A182 F22.
WC weldable castings
LCB / LCC (ASTM a352) low temperature carbon steel
1. Chemical Composition Requirements
Chemical Composition of ASTM A217 Castings, % | |||||||||
Grade | UNS | C | Mn | P | S | Si | Cr | Mo | Others |
WC1 | J12524 | ≤0.25 | 0.50-0.80 | ≤0.04 | ≤0.045 | ≤0.60 | – | 0.45-0.65 | *A |
WC4 | J12082 | 0.05-0.20 | 0.50-0.80 | ≤0.04 | ≤0.045 | ≤0.60 | 0.50-0.80 | 0.45-0.65 | *B |
WC5 | J22000 | 0.05-0.20 | 0.40-0.70 | ≤0.04 | ≤0.045 | ≤0.60 | 0.50-0.90 | 0.90-1.20 | *C |
WC6 | J12072 | 0.05-0.20 | 0.50-0.80 | ≤0.035 | ≤0.035 | ≤0.60 | 1.00-1.50 | 0.45-0.65 | *D |
WC9 | J21890 | 0.05-0.18 | 0.40-0.70 | ≤0.035 | ≤0.035 | ≤0.60 | 2.00-2.75 | 0.90-1.20 | *E |
WC11 | J11872 | 0.15-0.21 | 0.50-0.80 | ≤0.020 | ≤0.015 | 0.30-0.60 | 1.00-1.50 | 0.45-0.65 | *F |
C5 | J42045 | ≤0.20 | 0.40-0.70 | ≤0.04 | ≤0.045 | ≤0.75 | 4.00-6.50 | 0.45-0.65 | *G |
C12 | J82090 | ≤0.20 | 0.35-0.65 | ≤0.035 | ≤0.035 | ≤1.00 | 8.00-10.00 | 0.90-1.20 | *H |
C12A | J84090 | 0.08-0.12 | 0.30-0.60 | ≤0.025 | ≤0.010 | 0.20-0.50 | 8.0-9.5 | 0.85-1.05 | *H |
CA15 | J91150 | ≤0.15 | ≤1.00 | ≤0.040 | ≤0.025 | ≤1.50 | 11.5-14.0 | ≤0.50 | *I |
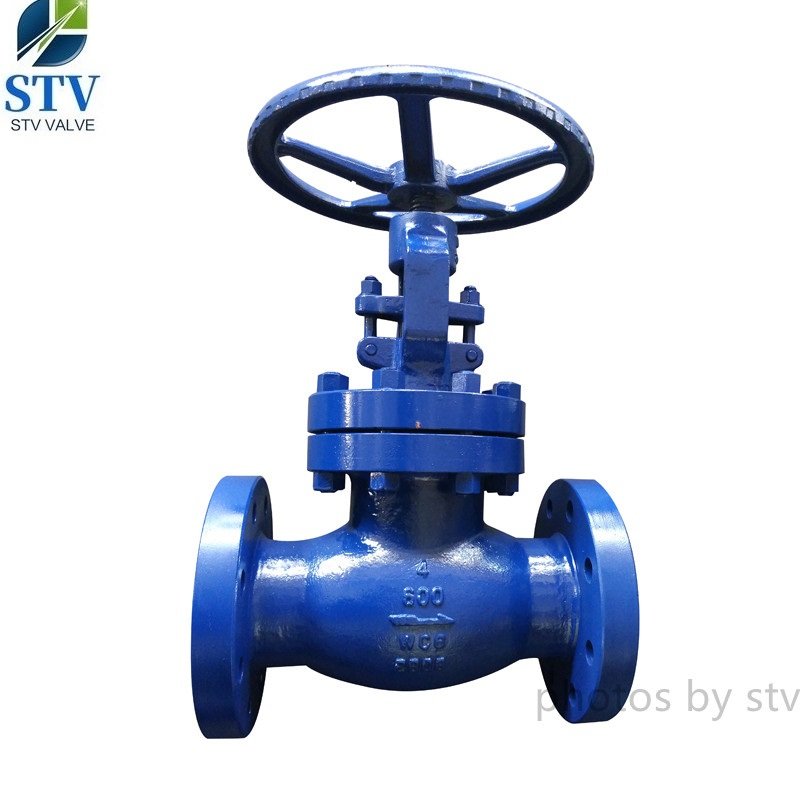
China ASTM A217 WC6 Globe Valve,4 Inch Globe Valve,Class 600 LB Globe Valve,RF Globe Valve,ASME B16.34 Globe Valve, BS 1873 Globe Valve, ASME B16.10 Globe Valve,carbon steel globe valve Manufacturer
*All values are maximum unless otherwise specified.
*A – Total Residual{Cu:≤0.50,Ni:≤0.50,Cr≤0.35,W≤0.10}:≤1.00. *B – Ni:0.70-1.10,Total Residual{Cu:≤0.50,W≤0.10}:≤0.60.
*C – Ni:0.60-1.00,Total Residual{Cu:≤0.50,W≤0.10}:≤0.60. *D – Total Residual{Cu:≤0.50,Ni:≤0.50,W≤0.10}:≤1.00.
*E – Total Residual{Cu:≤0.50,Ni:≤0.50,W≤0.10}:≤1.00. *F – Total Residual{Al:≤0.01,Cu:≤0.35,Ni:≤0.50,V≤0.03}:≤1.00.
*G – Total Residual{Cu:≤0.50,Ni:≤0.50,W≤0.10}:≤1.00. *H – Total Residual{Cu:≤0.50,Ni:≤0.50,W≤0.10}:≤1.00.
*I – Ni:≤0.40,Co:0.06-0.10,N:0.03-0.07,V:0.18-0.25,Total Residual{Al:≤0.02,Ti≤0.01,Zr≤0.01}. *J – Ni:≤1.00.
*Values from *A to *J shall be furnished with the unit “%”.
3. Heat Treatment
All castings shall receive a heat treatment proper to their design and chemical composition.
ASTM A217 castings shall be furnished in the normalized and tempered conditions; Grades WC1, WC4, WC5, WC6, and CA15 shall be tempered at 1100°F [595°C] min; Grades WC9, C5, C12, and WC11 shall be tempered at 1250°F [675°C] min; Grade C12A shall be thermally treated, either by normalizingand-tempering or by accelerated cooling from the austenitizing temperature by air blasting or liquid quenching, followed by tempering. C12A castings shall be austenitized at 1900-1975°F [1040-1080°C] and tempered at 1350-1470°F [730-800°C].
Heat treatment shall be performed after castings have been allowed to cool below the transformation range.
4. Quality Control
The surface of ASTM A217 castings (either valve, flange, fittings or other piping component) shall be visually examined and shall be free of sand, scale, cracks, and hot tears.
Hollow castings of Grade C12A, larger than NPS 4 [DN 100], and whose internal surfaces are not accessible to the visual examination above-mentioned, shall be examined by the ultrasonic examination prescribed in Supplementary Requirement S7.