Ball Valves
Introduction
This article contains all the information you need to know about Ball Valves.
Read further and learn more about:
What is a ball valve and how does it work?
Parts of a ball valve
Types of ball valves
Materials of construction of ball valves
Advantages and limitations of ball valves
And much more…
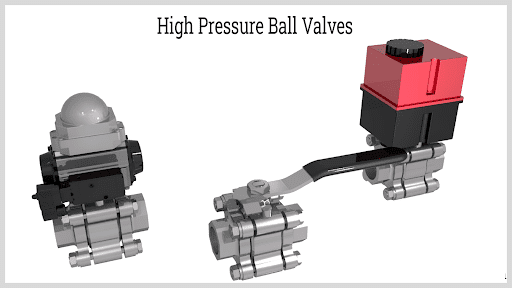
Chapter 1: What is a Ball Valve and How Does It Work?
A ball valve is a shut-off valve that allows, obstructs, and controls the flow of liquids, gases, and vapors in a piping system by rotating the ball having a bore inside the valve. The ball is mounted against two seats and has a shaft that connects it to the operating and control mechanism that rotates the ball. When the cross-section of the bore is perpendicular to the area of the flow, the fluid is not permitted to pass through the valve. The fluid flows through from the valve, and the fluid flow rate depends on the area of the bore exposed to the floor.
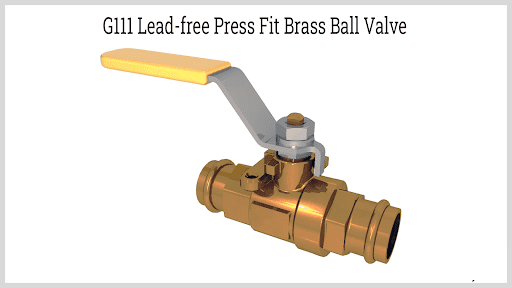
Ball valves are a type of quarter-turn valve along with plug valves and butterfly valves. They can be operated manually or by using an actuator. The simplest operation of a ball valve is through the use of a wrench or a lever manually turned by an operator. Torque is applied to rotate the lever arm by 90° by either clockwise or counterclockwise to open or close the valve. If the lever arm is parallel to the pipe, it indicates that the valve is open. If the lever arm is perpendicular to the pipe, it indicates that the valve is closed.
Ball valves come in many designs and features to satisfy various industrial needs. The standards and specifications for ball valves vary depending on the industry where it is utilized.
Chapter 2: Parts of a Ball Valve
The basic components of a ball valve include the following:
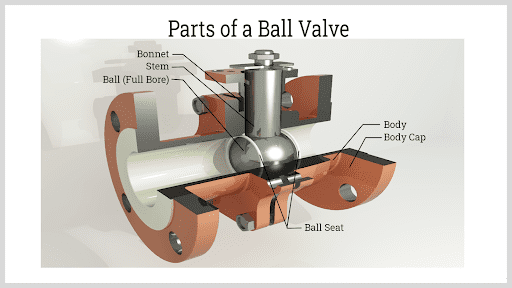
Valve housing
All internal components of a ball valve are contained inside the valve housing or the body. It is made of a hard and rigid metal, thermoplastic, or thermoplastic-lined metal that protects the components of the ball valve. It also allows access to the external control mechanism that rotates the ball.
Parts of a Ball Valve
Ball
The ball is a sphere that has a hole in its center. The hole in its center is called the bore. The bore serves as the flow opening of the fluid when the cross-section of the fluid flow path and the bore is coplanar. Otherwise, the flow is throttled. A ball valve may have a solid ball or a hollow ball. A solid ball has a constant opening diameter throughout its structure, which helps the fluid to smoothly flow at a constant velocity. A hollow ball, on the other hand, has a hollow internal structure, and the space inside it allows more fluid to pass through the valve. However, the larger space creates turbulence and high velocities. A hollow ball is more lightweight and cheap compared to a solid ball.
Shaft
The shaft connects the ball to the control mechanism that rotates the ball. The shaft has seals such as O-rings and packing rings to seal the shaft and the bonnet to avoid leakage of the fluid. The shaft may be manually operated by a lever or a handwheel or operated by an electric, pneumatic, or hydraulic actuation.
Bonnet
The bonnet is an extension of the valve housing that contains and protects the shaft and its packing. It may be welded or bolted to the body. It is also made of hard metal and it covers the opening made from connecting the shaft to the external control mechanism.
Seat
The valve seats provide sealing between the ball and its body. The upstream seat is adjacent to the inlet side of the valve. The downstream seat is found on the opposite side of the upstream seat which is adjacent to the discharge side of the valve.
GET YOUR COMPANY LISTED BELOW
Chapter 3: Types of Ball Valves
Ball valves may be classified according to their housing assembly, ball design, and bore profile.
Housing Assembly
Housing Assembly
One-Piece Ball Valve
A one-piece ball valve has a single-piece cast body that houses the internal components of the ball valve. This eliminates the risk of leakage of the fluid from the valve. One-piece ball valves are the cheapest ball valves and always have a reduced bore. A welded one-piece ball valve is more common but cannot be dismantled for cleaning and repaired once damaged; therefore, it is only used for applications with a low possibility of particle build-up, and where sanitation is not a major concern. On the other hand, screwed one-piece ball valves can be cleaned, serviced, and repaired, but dismantling requires special tools.
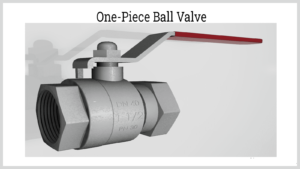
Split Body Ball Valves
Split Body Ball Valves are valves that are assembled on the sides of their balls. A split body ball valve may be a two-piece or a three-piece ball valve:
Two-Piece Ball Valve
A two-piece ball valve consists of housing divided into two pieces that are fitted together. The main piece contains the ball and a connection to one end, and the other piece holds the internal components together and has a connection to the other end. Two-piece housing is the most common type among ball valves. The two parts can be dismantled for cleaning, maintenance, and inspection but it requires removal of the valve from the pipe.
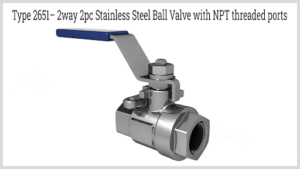
Three-Piece Ball Valve
A three-piece ball valve consists of the housing for the internal components of the valve which are fitted and held together by bolt connections to its two ends. The ends are threaded or welded to the main pipe.
Three-piece ball valves are used for applications that rely heavily on valves, that their maintenance activities must frequently be done. They can be cleaned and serviced easily and their seats and seals can be routinely replaced by just taking the valve body out without disturbing the two ends. Three-piece ball valves are commonly used in the food and beverage and pharmaceutical industries where sanitation is crucial to safety and product quality.
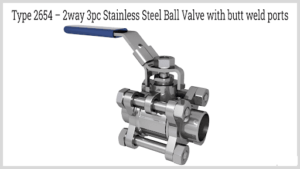
Top Entry Ball Valve
A top entry ball valve allows access to the internals of the valve by simply removing the bonnet on top of the valve. This allows in-line maintenance activities (i.e., dismantling, cleaning, inspection, and repairing the valve) without removing the ball valve from the main pipe.
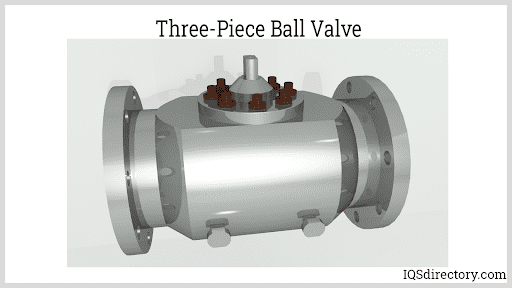
Ball Design
Floating Ball Valves
The floating ball is the most common ball design in ball valves. The ball is suspended inside the valve and free to move in a lateral direction when the valve is in a closed position. It is sandwiched between two seats that support the valve and hold it in place. The ball is connected to the shaft in a slot on one end while the other end is free. When the valve is in an open position, the shaft connection to the slot at the top of the ball prevents the ball from moving laterally.
The sealing action is only dependent on fluid pressure. During an operation of a floating ball valve, the inlet pressure of the fluid forces the ball to the outlet seat which prevents the fluid from escaping from the valve body. The fluid pressure on the ball and the seats are higher when the ball valve is in the closed position.
Floating ball valves have the simplest design. They come in smaller diameters and are suitable for liquids and gases operating under low to moderate pressures. The application of floating ball valves is limited by the amount of pressure the seats can handle. At high fluid pressure, the seats can be deformed from the pressure exerted by the ball which can affect the sealing characteristics of the valve under low pressure. Furthermore, the torque to rotate the stem depends on the force required to counteract the same fluid force acting on the ball and seals.
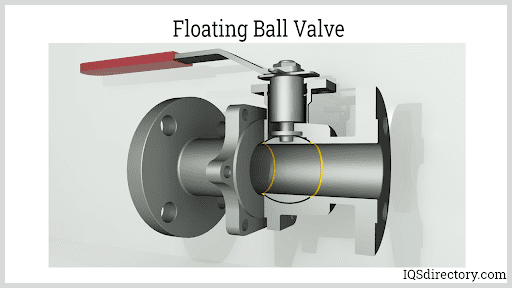
Trunnion Ball Valves
In a trunnion ball valve, the ball is supported by an additional shaft at its bottom which is called the trunnion. This holds the ball in its place and limits the movement of the ball to its axis. The ball can only move if the valve shaft rotates. Trunnion ball valves also feature spring-loaded seats. The inlet fluid pressure activates the springs towards the ball held by the trunnion, which creates a tight sealing.
Trunnion ball valves are available in small to large diameters, but it is more expensive than floating ball designs. They can operate efficiently in a wide range of pressures and they are ideal for high-pressure applications since the fluid pressure is also dissipated to the trunnion and the springs of the seats. Hence, they are easier to operate with a lower operating torque or a small actuator.
Vented Ball Valve
A vented ball valve is constructed and operates in the same way as a standard ball valve, except that the vented ball has small orifices drilled into its side. When the valve is closed, the orifice is directed to the outlet side of the valve. The drilled hole is used to vent trapped gases which causes a build-up of internal pressure inside the valve, to prevent leaking, valve failure, and explosion.
Vented ball valves are used in compressed air systems, cryogenic processing and conveying volatile liquids are also referred to as the “cryogenic valve” because of their usefulness in cryogenic processing.
Bore Profile
Full Bore Ball Valve
A full bore has a bore diameter similar to the pipe diameter. The flow area for the fluid for full bore valves remains constant, therefore the flow resistance offered by this type is very low. Minimal frictional loss is encountered during fluid flow; hence the pressure drop is low. A high pressure drop in a piping system causes pumping more difficult. However, since the bore diameter should be equal to the pipe size, it requires a larger ball size and housing which makes it more expensive than a reduced bore.
Full bore ball valves are easier to maintain and clean. In pipelines, the pipes are maintained and inspected by an operation called pigging. A spherical or cylindrical device called pigs is allowed to flow in the pipes to detect and remove any build-up without interfering with the fluid inside the pipeline. This operation is possible with an installed full-bore ball valve.
Full bore ball valves are also used in conveying liquids with mixed solids where flow restrictions cause the build-up of particles that can eventually cause separation of the mixtures that will flow through it.
Reduced Bore Ball Valve
A reduced bore has a bore diameter smaller by a pipe size than the (connection) pipe diameter. The actual reduction is determined by the agreement between the manufacturer and the customer. The flow area for the fluid becomes narrower at the downstream outlet, therefore there are frictional losses that are introduced which result in a pressure drop. Since the amount of flow discharge remains constant, the velocity increases with the decrease in the flow area.
Reduced bore ball valves are more common than full bore ball valves. They are used in applications where product flow rate and turbulence are not potential concerns and particle build-up is not likely to occur. The reduced bore is less expensive than the full bore since it requires a smaller ball size and housing. Compared to other types of valves, the reduced bore ball valves have relatively smaller pressure drop.
Segmented Ball Valve
A segmented ball valve has a V-shaped notch on its ball. A segmented ball valve has good flow rate control which depends on the ball rotation. Aside from that, it also has a good shut-off capability. The flow characteristic in a segment ball valve approaches an equal percentage flow characteristic. The flow rate in a segmented ball valve increases exponentially as the ball reaches its fully opened position.
Other Types of Ball Valve
Cavity-Filled Ball Valve
A cavity-filled ball valve has a seat design that fills the gap between the ball and its body. This eliminates the possibility of entrapped media or particle build-up over time around the ball which can cause contamination or blocking of the fluid flow. Cavity-filled ball valves are easier to clean and maintain.
Cavity-filled ball valves are valuable in industries where sanitation is crucial, such as in food, pharmaceutical, and bioprocessing industries. They are ideal in handling solid-liquid mixtures such as slurries.
Multi-Port Ball Valve
Multi-port ball valves are used in diverting, combining, splitting, or shutting off multiple fluid streams through the use of a ball with an L-shaped or T-shaped bore segmented through its middle. A flow upstream to the inlet of a multi-port valve can be split into multiple outlet streams. It can split a flow, but cannot distribute the flow to its outlet streams in pre-determined flow rates. It can also join multiple flow streams into a single stream, or simply change the direction of the fluid flow. The schematic diagram below shows possible flow configurations of an L-shaped and a T-shaped multi-port ball valve.
Chapter 4: Materials of Construction of Ball Valves
The ball valve‘s ball and its housing are commonly constructed from the following materials:
Brass
Brass is an alloy of copper and zinc that can be distinguished by its dull yellowish to reddish color, depending on the amount of zinc. It is the most common material for ball valves. Brass is a tough, strong, and durable metal that can withstand high temperatures and pressures. The copper in brass alloy has antimicrobial properties that inhibit the growth and reproduction of microbes on its surface. Brass has good chemical, corrosion, and biofouling resistance. It is inert to most acids, alkalis, and bases, except for solutions with high chlorine content. Chlorine can cause dezincification, a reaction where chloride ions strip away zinc from the alloy, causing a porous structure. Dezincification can drastically reduce the strength of the material.
Brass ball valves are not difficult to fabricate because of their malleability, and they are also easy to cast and weld. They are lighter and cheaper than steel ball valves. They are also easy to assemble in the piping system. Common applications of brass ball valves are in food, chemical, and oil and gas processing, and in conveying gaseous fluids. It is also safe to use in the delivery of potable drinking water.
Stainless Steel
Stainless steel is a type of steel that contains higher chromium content and some amounts of nickel. The chromium content of stainless steel makes it acquire a superior corrosion resistance. Stainless steel is known for its excellent strength, toughness, and durability. It also retains its strength in high temperatures and pressures.
Stainless steel ball valves are commonly constructed in 304 and 316 Stainless Steel grades. The 304 Stainless Steel has 18% chromium and 8% nickel, while 316 Stainless Steel has 18% chromium and 10% nickel and trace amounts of molybdenum. The combination of nickel and molybdenum makes the 316 Stainless Steel resistant to chlorides.
There are applications where the use of a stainless-steel ball valve is an excellent choice. They are used in swimming pools to handle chlorinated water. In harsh industrial environments such as desalination and petroleum refining plants, they offer better resistance to corrosive chemicals under high temperatures and pressures. In breweries, stainless steel pipes and valves are used to handle wort, a reactive liquid that is extracted during the mashing process.
Polyvinyl Chloride (PVC)
PVC is a tough, rigid and durable plastic material. Compared to brass and stainless-steel alloys, they generally have lower strength but they are cheaper. They are resistant to corrosion and most acids, bases, and salt solutions. However, they are not resistant to aromatic compounds and hydrocarbons. PVC ball valves have a lower temperature and pressure rating, for up to 150 psi and 140°F, respectively. Application of PVC ball valves includes plumbing, irrigation, and water distribution systems.
Chlorinated PVC (CPVC) is a type of PVC that has been chlorinated by a free radical reaction initiated by UV light. The chlorination of PVC results in higher temperature resistance. CPVC ball valves can handle higher temperatures of up to 200°F.
Polypropylene Ball Valve (PP)
PP is a tough, durable, lightweight, and flexible thermoplastic made from propylene monomer. It offers good resistance to most acids and bases, but has selective compatibility with organic substances and solvents. Its chemical resistance decreases with increasing temperatures. The maximum operating temperature of PP is 82°C. PP ball valves are suitable for regulating the flow of fluids with a wide range of viscosity. They are used as materials for ball valves in the manufacturing of sugar, fertilizers, chemicals, paper, and others.
Glass Fiber-Reinforced Polypropylene Ball Valve (GFPP)
In GFPPs, glass fibers are reinforced to polypropylene to increase its dimensional stability, rigidity, and chemical resistance, and to reduce the PP‘s coefficient of thermal expansion. Its heat deflection temperature is increased up to 150°C for a 40% GFPP at 264 psi. Reinforcement of glass fibers in PP increases cost-efficiency and makes it operate in more harsher and heavy-duty applications.
Polyvinylidene Difluoride Ball Valve (PVDF)
PVDF is a high purity, durable, thermoplastic fluoropolymer with high molecular weight. It is synthesized from gaseous vinylidene fluoride monomer by a free-radical polymerization process. It is also resistant to abrasion. This material has excellent chemical resistance that makes it suitable for handling reactive liquids and gaseous substances such as sulfuric acid, hydrochloric acid, nitric acid, hydrocarbons, fuels, and solvents that are aromatic, aliphatic, and halogenated in nature. It is used as a material for ball valves in industries such as water purification, wastewater treatment, and in food and pharmaceutical processing because of its good biofouling properties that is resistant to the growth of microbial films. It also remains unaffected by exposure to sunlight and UV. The maximum operating temperature of PVDF is around 115°C.
Polyethylene (PE)
PE is a durable, flexible, lightweight, and the most abundant thermoplastic. PE is compatible with most compounds, including strong acids and bases, and to some organic compounds including oils and alcohols. Its increasing crystallinity and density makes it more chemical resistant. PE ball valves are used in handling fluids in many manufacturing processes, as well as in water purification and wastewater treatment. The maximum operating temperature of PVDF is around 60°C.
Polyethylene Ball Valve
The seat is made from a softer material, such as an elastomeric material or plastic, for better sealing with the ball. A qualified seat material must also possess the following characteristics:
A low coefficient of friction
High compression strength
Creep resistance
High corrosion and chemical resistance
Compatibility with the flowing media
Examples of seat materials for ball valves are:
Polytetrafluoroethylene (PTFE), or also known as Teflon TM
TFM
Polyamide (Nylon)
Polyether ether ketone (PEEK)
UHMW Polyethylene
Acetal
A metal-seated ball valve has the ability to withstand higher temperatures and hydraulic pressures. They can handle more abrasive and corrosive fluids better.
Chapter 5: Advantages and Limitations of Ball Valves
The benefits of using a ball valve are the following:
Ball valves induce a low pressure drop compared to other types of valves since the flow has minimal restrictions. In liquids, a high pressure drop across a valve may result in turbulence and cavitation. Cavitation happens when the liquid pressure falls below the critical pressure, the vapor phase of the liquid is formed. As the pressure recovers, the bubbles collapse which damages the valve.
Since it only requires a one-quarter turn to fully shut off or open, the ball valves immediately restrict or allow flow. This advantage is important for controlling the liquid level of a tank or a reservoir.
A small amount of torque or a small actuator is needed to rotate the ball valve.
Lubrication is unnecessary because of the surface properties of the seats.
Ball valves offer a reduced chance of leakage because the ball seals tightly against the seats. The sealing action is done by fluid pressure.
Several ball valve designs are available to satisfy a specific application. Some ball valve designs feature pressure relief, variable flow rate control, flow splitting, and mixing, etc.
Ball valves are relatively cheaper.
There are several limitations the user must remember to preserve the functionality of the ball valve:
Throttling is possible in ball valves, but it should be sustained for a long time. When the ball valve is in a throttling position, the seats are exposed to the high-velocity fluid flow and more compressive force, which causes erosion. Therefore, it is not advisable for throttling applications. Standard ball valves may be used in throttling low pressure gases. Segmented ball valves may be used in limited throttling applications. However, advanced ball valves with modified designs or seats made from engineered materials that are suitable for throttling applications are commercially available.
Application is limited by the maximum allowable working temperature of the seats. For higher temperatures, metal or ceramic seats are an alternative.
Suspended particles may build up between the body and ball, causing leakage, erosion, and valve failure. Hence, it is advised to do frequent maintenance on ball valves handling slurries and suspensions.
Conclusion
Ball valves are shut-off valves used to allow or obstruct the flow of fluids by rotating the ball having a bore inside it by 900. They can be operated manually or by an actuator.
Ball valves consist of the ball, shaft, and seat which are contained in the valve housing. The ball is placed between two seats and has a stem that connects it to the operating mechanism.
Types of ball valves are classified according to their housing assembly, ball design, and bore profile. Ball valves come in many designs and features to satisfy the needs of a specific industry.
As the housing is divided into many pieces, the cleaning and maintenance of the ball valves get easier but more expensive to acquire.
There are different types of ball design to select from, depending on the working pressure it will be installed to.
A smaller bore diameter has a larger pressure drop across the valve, which makes pumping difficult and more expensive. The ball may have a multiport bore which can be used for splitting and combining flow rates and diverting flow directions.
The material for ball valves must be hard, tough, and rigid. The seats must have a low coefficient of friction, high compressive strength, and compatibility with the working fluid. However, the application of ball valves is limited by the working temperature of the seats.
Ball valves are easy to operate and activated and offer minimal risk to leakage.
Throttling is not advisable for ball valves.
Proper maintenance must be done to avoid particle build-up between the ball and the body.
GET YOUR COMPANY LISTED BELOW
“Original article found here“. Thank you very much for your interest in reading our article。